在PCBA智造領域,每一塊電路板的品質都是終端產品生命力的根基。行業調查顯示,68%的電子設備故障源于PCBA環節,其癥結往往潛伏于四大環節:設計驗證不足導致的工藝性缺陷、替代料濫用引發的兼容性風險、過程監控盲區造成的批量異常、以及售后追溯體系缺失帶來的改進遲滯。這些頑疾如同多米諾骨牌,隨時可能引發交付延期與商譽危機。
深圳宏力捷電子憑借20年技術深耕,獨創"三維質量防御體系",通過19道質量閘口將直通率推升至99.9%的行業峰值。這個數字背后,是20年技術積淀形成的五大智造體系在支撐。
一、全流程數字化管控系統
我們的ERP-MES雙系統實現了從訂單到交付的全程可視化追蹤。在物料入庫階段,通過智能貨架自動比對元件批次與BOM清單,將物料錯配風險降至0.02%以下。生產過程中,每片板卡都帶有專屬ID芯片,實時記錄120+關鍵工藝參數,確保問題可追溯至具體設備與操作員。
二、進口設備集群精密協作
車間配備的西門子SX系列高速貼片機,采用3D激光校準技術實現01005元件(0.4×0.2mm)±25μm的貼裝精度。搭配ERSA回流焊機的16溫區氮氣保護系統,可將焊接峰值溫度波動控制在±1.5℃以內。DIP生產線配置的自動光學檢測儀(AOI)具備0.02mm²的缺陷識別能力,相當于在A4紙上發現半粒芝麻大小的異常。
三、六階品控保障體系
1. 來料檢驗:X射線檢測儀深度篩查元器件內部結構
2. 首件確認:三維坐標測量儀執行168項參數驗證
3. 過程監控:每2小時抽樣進行紅墨水試驗驗證焊接強度
4. 功能測試:自主研發的ICT/FCT復合測試架實現100%通電檢測
5. 老化測試:72小時高溫高濕環境模擬測試
6. 終檢包裝:工業內窺鏡進行BGA焊點360°檢測
四、軍工級物料管理體系
我們與TI、村田、三星等30余家原廠建立戰略合作,中央倉儲采用恒溫恒濕(23℃±1,40%RH)環境儲存敏感元件。針對汽車電子等特殊領域,實施MSD器件真空封裝管理,開封后4小時內完成貼裝作業。
五、持續工藝優化機制
每月投入營收的5%用于技術升級,自主研發的工藝參數優化系統(PPOS)已積累超過50萬組焊接曲線數據。通過機器學習算法,可針對不同板型自動匹配最佳溫度曲線,將二次回流不良率降低82%。
正是這種"技術偏執",讓宏力捷在汽車電子領域創造了連續18個月零客訴的紀錄。我們的工程團隊可為客戶提供DFM可制造性分析報告,提前規避127種常見設計缺陷。從樣品到量產,始終踐行"零缺陷傳遞"的質量理念。
【常見問題】
Q:如何確保BOM清單準確性?
A:采用智能BOM解析系統,自動比對300+元器件參數數據庫
Q:最小可加工元件尺寸?
A:支持01005封裝(0.4×0.2mm)及0.3mm pitch BGA元件
Q:交期如何保障?
A:通過安全庫存機制+彈性產能配置,常規訂單5-7天交付
在工業4.0時代,宏力捷電子正以"智造精度"重新定義PCBA質量標準。選擇我們,不僅是選擇一家PCBA加工廠,更是選擇整個供應鏈的質量承諾。
深圳宏力捷推薦服務:PCB設計打樣 | PCB抄板打樣 | PCB打樣&批量生產 | PCBA代工代料
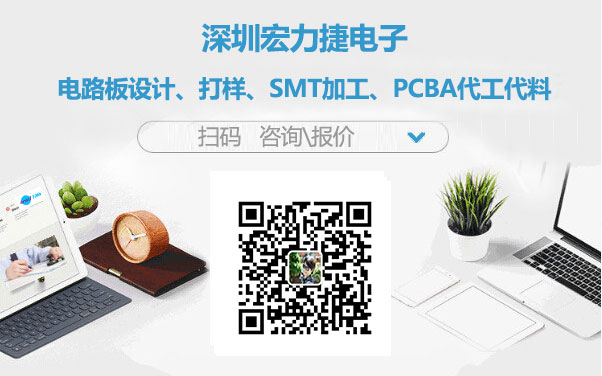